Metal casting is widely used in the manufacturing process. So, what are the types of metal casting and what are the processes of metal casting service?
Metal casting is the process of pouring liquid metal into a mold through a hollow channel called a gate. Then cool the metal and mold, and remove the metal parts. Casting is most commonly used to manufacture complex shapes, while other methods are difficult or uneconomical.
The metal casting process has been known for thousands of years and has been widely used in carving (especially in bronze), precious metals in jewelry. Highly engineered castings have been found in 90% of durable goods, including automotives, trucks, aerospace, trains, mining and construction equipment, oil wells, electrical appliances, pipelines, fire hydrants, wind turbines, nuclear power plants, medical equipment, toys, and more.
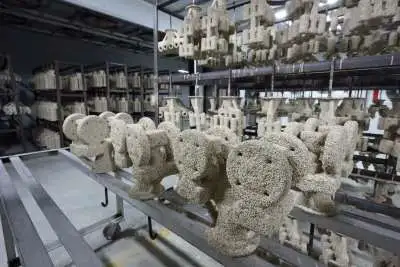
The types and modeling methods of metal casting are traditionally divided into:
① Ordinary sand casting includes three types: wet sand mold, dry sand mold, and chemically hardened sand mold. The investment cost of sand casting is low, the mold is easy to make (there are no restrictions on mold methods such as foam, wood, plastic, metal, etc.), and the production and operation costs are also low. The disadvantage is that employees require certain skills, and immature processes can easily lead to high scrap rates.
② Special casting can be further divided into two categories based on the molding materials: special casting with natural mineral sand and gravel as the main molding material (such as investment casting, mud casting, shell casting in casting workshops, negative pressure casting, full mold casting, ceramic mold casting, etc.) and special casting with metal as the main molding material (such as metal mold casting, pressure casting, continuous casting, low-pressure casting, centrifugal casting, etc.).
Metal casting processes typically include:
- Preparation of molds (containers that turn liquid metal into solid castings), which can be divided into sand molds, metal molds, ceramic molds, mud molds, graphite molds, etc. according to the materials used, and can be divided into disposable molds, semi permanent molds, and permanent molds according to the number of uses. The quality of mold preparation is the main factor affecting the quality of castings;
- The melting and pouring of cast metals, including iron casting, steel casting, and cast non-ferrous alloys;
- Casting treatment and inspection, including removing foreign objects from the core and surface of the casting, cutting off the sprue and riser, grinding burrs and burrs, as well as heat treatment, shaping, rust prevention treatment, and rough machining.
This article is reprinted from: https://steelcastingmfg.com/
0 Comments