Machining accuracy is the degree to which the three geometric parameters of the actual size, shape, and position of the machined part surface conform to the ideal geometric parameters required by the drawing.
The ideal geometric parameters, in terms of size, are the average size; in terms of surface geometry, they are absolute circles, cylinders, planes, cones and straight lines, etc.; in terms of mutual positions between surfaces, they are absolute parallelism , vertical, coaxial, symmetrical, etc. The deviation between the actual geometric parameters of the part and the ideal geometric parameters is called the machining error.
The Concept Of CNC Machining Accuracy
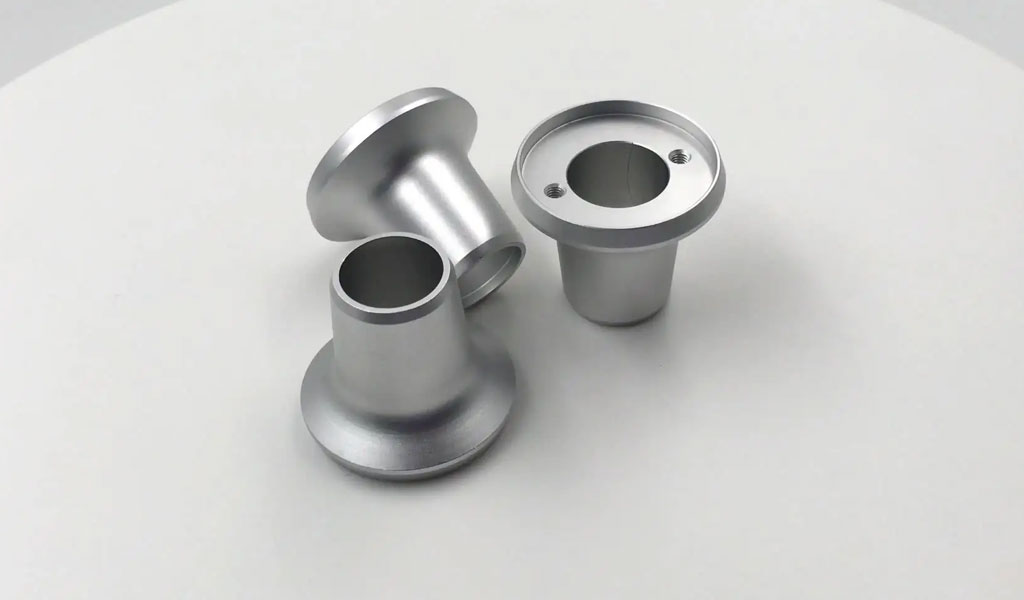
Machining accuracy is mainly used to produce products, and both machining accuracy and machining error are terms for evaluating the geometric parameters of the machined surface. The machining accuracy is measured by the tolerance grade, the smaller the grade value, the higher the precision; the machining error is expressed by a numerical value, the larger the numerical value, the greater the error. High machining accuracy means small machining error, and vice versa.
There are 20 tolerance grades from IT01, IT0, IT1, IT2, IT3 to IT18. Among them, IT01 represents the highest Machining accuracy of the part, and IT18 represents the lowest Machining accuracy of the part. Generally speaking, IT7 and IT8 have medium Machining accuracy. level.
The actual parameters obtained by any Machining method will not be absolutely accurate. From the perspective of the function of the part, as long as the Machining error is within the tolerance range required by the part drawing, the Machining accuracy is considered to be guaranteed.
The quality of the machine depends on the Machining quality of the parts and the assembly quality of the machine. The Machining quality of the parts includes two parts: the Machining accuracy and the surface quality of the parts.
Machining accuracy refers to the degree to which the actual geometric parameters (size, shape, and position) of a part after machining conform to the ideal geometric parameters. The difference between them is called machining error. The size of the machining error reflects the level of machining accuracy. The larger the error, the lower the machining accuracy, and the smaller the error, the higher the machining accuracy.
Relevant Content Of Machining Accuracy
(1) Dimensional accuracy
Refers to the degree of conformity between the actual size of the processed part and the center of the tolerance zone of the part size.
(2) Shape accuracy
Refers to the degree of conformity between the actual geometric shape of the processed part surface and the ideal geometric shape.
(3) Position accuracy
Refers to the difference in actual position accuracy between the relevant surfaces of the machined parts.
(4) Mutual relationship
Usually, when designing machine parts and specifying the machining accuracy of parts, attention should be paid to controlling the shape error within the position tolerance, and the position error should be smaller than the size tolerance. That is, for precision parts or important surfaces of parts, the shape accuracy requirements should be higher than the position accuracy requirements, and the position accuracy requirements should be higher than the dimensional accuracy requirements.
Causes Of Influence
(1) Machining principle error
The machining principle error refers to the error generated by using an approximate blade profile or an approximate transmission relationship for Machining. Machining principle errors mostly appear in the Machining of threads, gears, and complex curved surfaces. In Machining, approximate Machining is generally used to improve productivity and economy on the premise that the theoretical error can meet the requirements of Machining accuracy.
(2) Adjustment error
The adjustment error of the machine tool refers to the error caused by inaccurate adjustment.
(3) Machine tool error
Machine tool error refers to the manufacturing error, installation error and wear of the machine tool. It mainly includes the guiding error of the machine tool guide rail, the rotation error of the machine tool spindle, and the transmission error of the machine tool transmission chain.
How To Improve The Machining Accuracy Of Parts
(1) Adjust the process system
Single loose samples can be adjusted by trial cutting, but this method has low production efficiency. The adjustment method obtains the required size by pre-adjusting the relative positions of the machine tool, fixture, workpiece and tool, which has high efficiency and is suitable for mass production.
(2) Reduce machine error
It is mainly achieved by improving the manufacturing accuracy of the main shaft components and properly preloading the rolling bearings.
(3) Reduce the transmission error of the transmission chain
The number of transmission parts is small, the transmission chain is short, and the transmission accuracy is high; the use of reduced speed transmission is an important principle to ensure transmission accuracy, and the closer to the end of the transmission pair, the smaller the transmission ratio should be.
In addition, the machining accuracy of parts can also be improved by reducing tool wear, reducing the force deformation of the process system, reducing the thermal deformation of the process system, and reducing residual stress.
What Is The Maximum Machining Accuracy Of The CNC Machine
(1) Turning
The turning precision is generally IT8-IT7, and the surface roughness is 1.6-0.8μm.
The machining accuracy of rough turning can only reach IT11, and the surface roughness is Rα20-10μm; the machining accuracy of semi-finishing and finishing turning can reach IT10-IT7, and the surface roughness is Rα10-0.16μm; the high-precision lathe can make the machining accuracy reach IT7- IT5, the surface roughness is Rα0.04-0.01μm, this kind of turning is called “mirror turning”.
(2) Milling
The machining accuracy of milling can generally reach IT8-IT7, and the surface roughness is 6.3-1.6μm.
Machining accuracy IT11-IT13 during rough milling, surface roughness 5-20μm; Machining accuracy IT8-IT11 during semi-finish milling, surface roughness 2.5-10μm; Machining accuracy IT16-IT8 during fine milling, surface roughness 0.63- 5 μm.
(3) planing
The planing precision can generally reach IT9-IT7, and the surface roughness is Ra6.3-1.6μm.
The Machining accuracy of rough planing can reach IT12-IT11, and the surface roughness is 25-12.5μm; the Machining accuracy of semi-fine planing can reach IT10-IT9, and the surface roughness is 6.2-3.2μm; The roughness is 3.2-1.6μm.
(4) Grinding
Grinding is usually used for semi-finishing and finishing, the accuracy can reach IT8-IT5 or even higher, and the surface roughness is generally 1.25-0.16μm.
The surface roughness of precision grinding is 0.16-0.04μm; the surface roughness of ultra-precision grinding is 0.04-0.01μm; the surface roughness of mirror grinding can reach below 0.01μm.
(5) Drilling
The machining accuracy of drilling is low, generally only up to IT10, and the surface roughness is generally 12.5-6.3 μm. After drilling, reaming and reaming are often used for semi-finishing and finishing.
(6) Boring
The machining accuracy of precision boring can reach IT7-IT6, and the surface roughness is 0.63-0.08μm; the boring accuracy of steel materials can generally reach IT9-IT7, and the surface roughness is 2.5-0.16μm.
0 Comments